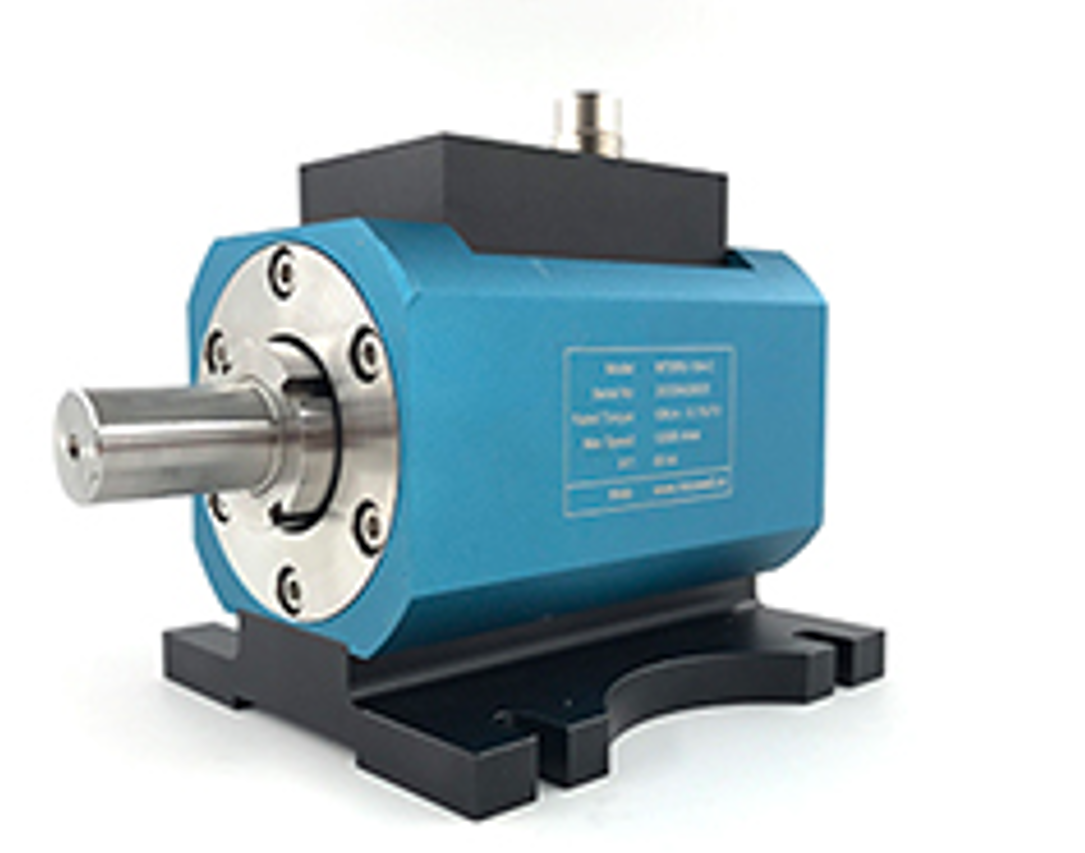
In the rapidly evolving world of industrial automation, electric vehicles, and renewable energy systems, the demand for precise motor testing solutions has never been higher. At the intersection of innovation and reliability lie hysteresis-based technologies—hysteresis brakes, hysteresis dynamometers, hysteresis clutches—and their integration into comprehensive motor test systems. These tools are not just components; they are the backbone of quality assurance for industries that depend on accuracy, repeatability, and durability. Let’s explore how these technologies redefine performance validation and why they are indispensable in modern engineering.
The Fundamentals of Hysteresis Technology
Hysteresis devices operate on the principle of magnetic hysteresis, where energy loss occurs in magnetic materials subjected to alternating magnetic fields. This phenomenon enables precise control over torque and load without physical contact, reducing wear and maintenance. Unlike traditional friction-based systems, hysteresis mechanisms offer smooth operation, zero mechanical degradation, and exceptional repeatability. This makes them ideal for applications requiring long-term reliability, such as automotive testing, aerospace component validation, or industrial motor calibration.
Hysteresis Brakes: Silent Guardians of Controlled Deceleration
Hysteresis brakes are the unsung heroes in scenarios requiring controlled stopping power. Whether it’s testing the endurance of an electric vehicle’s regenerative braking system or simulating real-world load conditions for industrial machinery, these brakes deliver consistent torque without the variability of friction-based alternatives. Their non-contact design eliminates particulate generation, making them perfect for cleanroom environments like semiconductor manufacturing or medical device assembly. Key advantages include:
- Torque accuracy within ±1% of full scale
- Instant response to control signals
- Minimal thermal drift even under continuous operation
- Customizable cooling solutions for high-power applications
Aerospace engineers, for instance, rely on hysteresis brakes to test actuator systems for flight control surfaces, where precision and failure resistance are non-negotiable.
Hysteresis Dynamometers: Capturing Every Nuance of Power Output
When it comes to measuring motor performance, hysteresis dynamometers set the gold standard. These devices absorb and measure mechanical power while simulating real-world loads, enabling engineers to validate efficiency, thermal behavior, and dynamic response. Their ability to maintain stable torque across varying speeds makes them indispensable for testing EV drivetrains, wind turbine generators, or high-speed industrial spindles.
Consider the challenge of developing a next-generation electric motorcycle. Engineers use hysteresis dynamometers to replicate hill climbs, sudden accelerations, and regenerative braking cycles, collecting data on energy consumption, heat dissipation, and component stress. The dynamometer’s inherent linearity ensures that test results correlate directly with real-world performance, eliminating guesswork during R\u0026D.
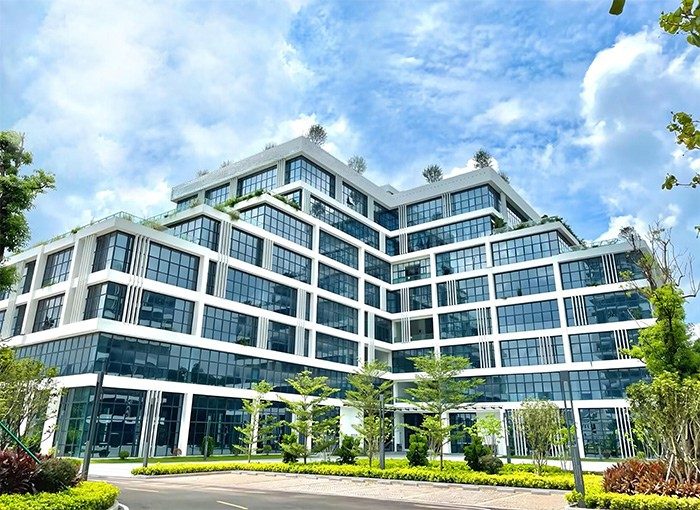
Hysteresis Clutches: Seamless Power Transfer in Critical Systems
Hysteresis clutches excel in applications requiring smooth engagement and precise torque control. From robotic assembly lines to precision printing machinery, these clutches enable slip-free power transmission with programmable torque limits. Their ability to handle high inertia loads without physical contact makes them ideal for protecting sensitive equipment from overloads.
In pharmaceutical packaging lines, for example, hysteresis clutches ensure consistent tension in labeling systems, preventing costly misalignments or material waste. The absence of brushes or friction plates translates to maintenance-free operation over thousands of hours—a critical factor in 24/7 production environments.
Motor Dynamometers: Beyond Basic Performance Metrics
Modern motor dynamometers are no longer just about measuring RPM and torque. Integrated with hysteresis load banks and advanced sensors, these systems provide a 360-degree view of motor behavior. Key capabilities include:
- Real-time efficiency mapping across operating ranges
- Harmonic distortion analysis for power quality assessment
- Transient response testing under simulated grid fluctuations
- NVH (Noise, Vibration, Harshness) profiling
Take the case of a solar pump manufacturer aiming to optimize energy usage. A motor dynamometer system can simulate varying sunlight conditions, measuring how the pump’s motor adjusts its power draw while maintaining hydraulic performance. This data directly informs design improvements that reduce energy waste by up to 15%.
The Rise of Integrated Motor Test Systems
Today’s motor test systems are holistic platforms combining hysteresis components, data acquisition modules, and AI-driven analytics. These turnkey solutions automate complex test sequences, from ISO efficiency certifications to accelerated life testing. A typical system might integrate:
1. A hysteresis dynamometer for load simulation
2. Precision power analyzers with 0.05% accuracy
3. Thermal imaging cameras for hotspot detection
4. Cloud connectivity for remote monitoring and benchmarking
For an EV manufacturer, such a system could automate the validation of 50 motor variants per week, comparing each unit’s performance against digital twins and flagging deviations in real time. Machine learning algorithms predict bearing wear or insulation degradation years before failure, transforming maintenance strategies from reactive to predictive.
Industry-Specific Applications
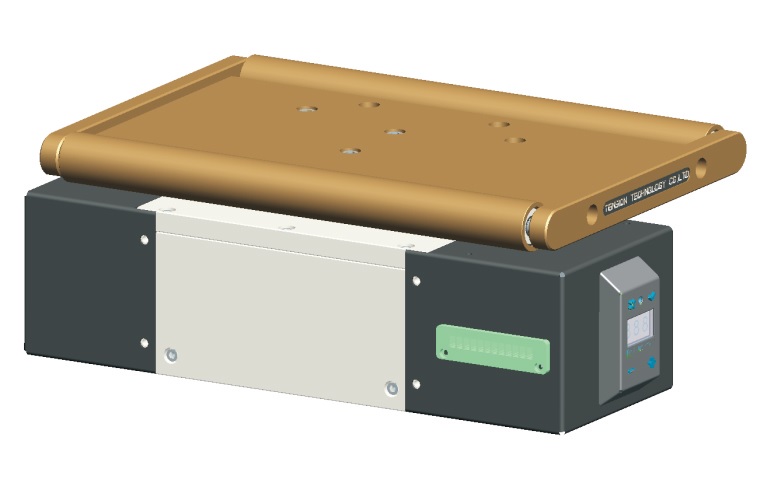
Automotive: As electric vehicles dominate the market, hysteresis-based test systems validate everything from window lift motors (ensuring silent operation) to traction inverters (testing fault tolerance during voltage spikes). Regenerative braking systems undergo millions of simulated stop-start cycles to guarantee consistency over a vehicle’s lifespan.
Aerospace: Helicopter tail rotor actuators are subjected to extreme torque reversals in environmental chambers replicating -50°C to +85°C conditions. Hysteresis dynamometers measure response times down to milliseconds, critical for flight safety.
Renewables: Wind turbine generators are tested under synthetic wind profiles, assessing how well they maintain grid compliance during gusting and lulls. Hysteresis load banks dissipate megawatts of energy while capturing data for certification bodies like UL or TÜV.
Consumer Electronics: The vibration motor in a smartphone undergoes precise torque testing to ensure haptic feedback remains consistent after 500,000 actuations. Hysteresis brakes apply programmable resistance to simulate screen swipes under different temperatures and humidity levels.
Choosing the Right Partner for Motor Test Solutions
Investing in hysteresis-based test equipment requires careful consideration:
- Scalability: Can the system grow with your product lineup?
- Compliance: Does it support regional standards (IEC, SAE, JIS)?
- Software Ecosystem: Are analysis tools compatible with your PLM/MES systems?
- Support: What level of calibration and training is provided?
Leading suppliers offer modular designs—start with a basic dynamometer for torque-speed curves, then add battery emulators for hybrid system testing or acoustic chambers for noise profiling. Look for systems with open API architectures, allowing custom test scripts and third-party instrument integration.
The Road Ahead: Smart Manufacturing and IIoT Integration
As Industry 4.0 reshapes production floors, motor test systems evolve into intelligent nodes within the Industrial Internet of Things (IIoT). Imagine a hysteresis dynamometer that not only tests motors but also:
- Auto-adjusts test parameters based on real-time production data
- Shares efficiency metrics with procurement teams to optimize supplier selection
- Uses digital twins to predict how design changes will affect warranty claims
- Integrates blockchain ledgers for tamper-proof certification records
In smart factories, these systems communicate with robotic assemblers, triggering recalibration when motor performance drifts beyond predefined thresholds. Predictive maintenance algorithms analyze historical test data to schedule component replacements before they impact throughput.
Precision motor testing for appliances : Elevating Quality in an Electrified World
From the subtle hum of a drone’s propulsion motor to the megawatt roar of a tidal power generator, hysteresis-based testing technologies ensure that every rotation counts. They empower engineers to push boundaries while maintaining unwavering quality—whether developing a hypercar’s axial flux motor or refining the servo that positions silicon wafers with nanometer precision.
In choosing hysteresis brakes, dynamometers, and integrated test systems, manufacturers don’t just buy equipment—they invest in a legacy of reliability. As industries march toward electrification and autonomy, those who master the art of precision testing today will define the performance standards of tomorrow.
The question is no longer whether to adopt these technologies, but how quickly you can integrate them into your innovation pipeline. After all, in the race to build better machines, the difference between leading and following often comes down to how well you can measure—and improve—what others merely assume.