In the rapidly evolving landscape of industrial automation and electric motor development, the demand for precision testing and control systems has never been higher. From automotive engineering to renewable energy applications, professionals rely on cutting-edge technologies like hysteresis brakes, dynamometers, clutches, and integrated motor test systems to push the boundaries of performance and reliability. This article explores how these critical components form the backbone of modern engineering workflows while delivering unparalleled accuracy and adaptability.
THE SCIENCE BEHIND HYSTERESIS TECHNOLOGY
At the heart of advanced torque management systems lies the principle of hysteresis – a phenomenon where magnetic materials exhibit lagged response to applied magnetic fields. This natural property is ingeniously harnessed in three key industrial components:
1. HYSTERESIS BRAKES: THE FRICTIONLESS WORKHORSE
Unlike traditional mechanical brakes that wear down through physical contact, hysteresis brakes operate through electromagnetic induction. When Web positioning systems at a leading EV manufacturer needed to test regenerative braking systems without introducing mechanical variance, they implemented hysteresis brakes capable of:
- Generating consistent torque proportional to excitation current
- Enabling smooth engagement across 0-10,000 RPM ranges
- Operating maintenance-free for over 20,000 test cycles
This solution eliminated particulate contamination in clean room environments while providing precise dynamic load simulation for battery stress testing.
2. HYSTERESIS DYNAMOMETERS: MEASURING TOMORROW'S POWER TODAY
Modern hysteresis dynamometers have revolutionized how R\u0026D teams validate motor performance. A recent case study from a wind turbine manufacturer revealed how their 450kW hysteresis dynamometer system:
- Achieved torque measurement accuracy within ±0.25% of reading
- Enabled four-quadrant testing for full motor/generator mode analysis
- Integrated with AI-powered predictive maintenance software
By simulating actual field conditions from arctic cold starts to desert thermal stress, the system helped reduce prototype validation cycles by 40%.
3. HYSTERESIS CLUTCHES: WHERE PRECISION MEETS DURABILITY
In high-speed packaging machinery applications, a prominent automation supplier replaced traditional friction clutches with hysteresis models to address their clients' needs for:
- Slip-free torque transmission up to 15,000 RPM
- Contactless operation eliminating mechanical wear
- Microsecond-level response times for precision positioning
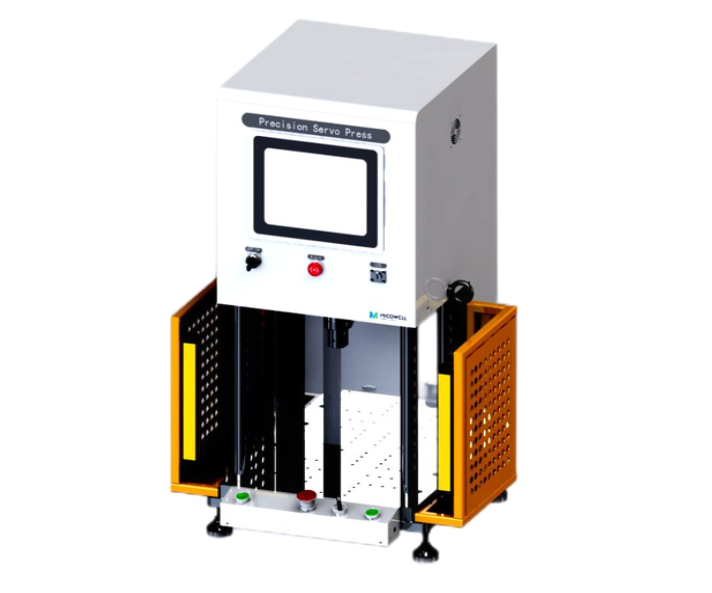
The result was a 68% reduction in unplanned downtime across 37 production lines while maintaining positional accuracy within 5 arc-seconds.
MOTOR TESTING SYSTEMS: THE ARCHITECTURE OF INNOVATION
Modern motor test equipment has evolved into sophisticated ecosystems that combine mechanical, electrical, and software components. A typical advanced motor test system might integrate:
- MULTI-AXIS DYNAMOMETERS
Capable of simultaneously measuring torque, rpm, temperature, and vibration across multiple mechanical connections
- REGENERATIVE POWER ANALYZERS
Capturing detailed energy flow data while recycling up to 95% of test energy back into facility power grids
- ENVIRONMENTAL SIMULATION CHAMBERS
Replicating operating conditions from -55°C to +180°C with altitude simulations up to 15,000 meters
- AI-DRIVEN TEST SEQUENCERS
Automatically adapting test parameters based on real-time performance data and historical trends
Aerospace engineers recently leveraged such a system to certify electric propulsion units for hybrid helicopters, compressing a 12-month certification process into just 7 months while collecting 83% more performance data points.
ADVANCEMENTS IN TEST METHODOLOGY
The latest generation of motor test systems incorporates several groundbreaking technologies:
DYNAMIC MAPPING ALGORITHMS
Real-time creation of efficiency heat maps across entire operating envelopes allows engineers to visually identify optimal performance zones. During testing of a new servo motor design, this technology revealed a previously undetected 11% efficiency gain at partial load conditions.
CLOUD-BASED TEST Electrical device assembly
Secure remote access capabilities enable global engineering teams to collaborate on test campaigns. A multinational automotive supplier reported a 29% reduction in development time after implementing cloud-connected test cells across facilities in Germany, China, and Texas.
CYBER-PHYSICAL TESTING
By combining Torque testing for stepper motors with digital twin simulations, engineers can run hybrid validation tests that combine real-world measurements with predictive modeling. This approach allowed a robotics firm to validate 78% of their motor control algorithms before physical prototypes were available.
APPLICATIONS DRIVING INNOVATION
The versatility of modern hysteresis and motor testing systems is demonstrated through diverse industry applications:
ELECTRIC VEHICLE DEVELOPMENT
- Battery emulation testing for regenerative braking systems
- Endurance testing of traction motors under simulated road loads
- Thermal management validation for extreme climate operation
AEROSPACE SYSTEMS
- Testing of fly-by-wire actuator motors under vibration profiles
- Validation of satellite reaction wheel longevity
- Certification testing for electric aircraft propulsion systems
INDUSTRIAL AUTOMATION
- Lifetime testing of robotic joint actuators
- Precision validation of CNC spindle motors
- Energy efficiency optimization for conveyor systems
RENEWABLE ENERGY
- Wind turbine pitch control motor certification
- Solar tracking system durability testing
- Tidal generator torque response analysis
THE COST OF INACCURACY: WHY PRECISION MATTERS
Recent industry studies reveal the dramatic impact of testing precision:
- A 1% improvement in motor efficiency can save a manufacturing plant $36,000 annually in energy costs
- Undetected torque ripple in medical imaging equipment motors led to $2.3M in warranty claims
- Inadequate testing of drone propulsion systems resulted in a 13% failure rate during field operations
These sobering statistics underscore why leading organizations invest in advanced test solutions capable of detecting sub-0.5% efficiency variations and microscopic torque fluctuations.
FUTURE HORIZONS: EMERGING TECHNOLOGIES
As industries push toward electrification and smart manufacturing, testing systems are evolving to address new challenges:
WIRELESS TORQUE MEASUREMENT
Embedded sensor systems that eliminate slip ring limitations in high-RPM applications
CRYOGENIC TEST CAPABILITIES
Specialized chambers for superconducting motor development operating near absolute zero
PHOTONIC TORQUE SENSORS
Fiber-optic based measurement systems immune to electromagnetic interference
AUTONOMOUS TEST OPTIMIZATION
Machine learning algorithms that automatically design test protocols based on product requirements
These innovations promise to further compress development cycles while improving product reliability across industries.
SELECTING THE RIGHT SOLUTION
When evaluating hysteresis and motor testing systems, consider these critical factors:
- Torque range and speed compatibility with target applications
- Measurement accuracy class and certification requirements
- Integration capabilities with existing test infrastructure
- Software flexibility for custom test sequences
- Energy recovery efficiency and facility impact
- Service network responsiveness and technical support
Leading suppliers now offer configurable systems that can scale from benchtop R\u0026D units to megawatt-class production test cells, ensuring organizations of all sizes can access cutting-edge testing capabilities.
The silent revolution occurring in motor testing laboratories and production facilities worldwide is fundamentally changing how we develop and validate motion technologies. From the nano-scale precision of hysteresis components to the overwhelming data capabilities of modern test systems, these technologies form an invisible backbone supporting innovation across every sector of advanced manufacturing. As industries continue their march toward electrification and intelligent automation, the organizations that strategically invest in these testing solutions will undoubtedly lead the charge into our technological future.
By embracing Motor lifetime testing systems , flexibility, and intelligence of modern hysteresis and motor testing systems, engineering teams can not only meet today's challenges but also unlock possibilities for innovations we've yet to imagine. The question is no longer whether to implement these solutions, but how quickly organizations can leverage them to gain competitive advantage in an increasingly demanding technological landscape.